Bonjour,
Je cherche actuellement à déterminer si mon tirant soumis à une traction ne dépasse pas la limite élastique.
Schématiquement, un écrou hydraulique est en appui au travers de sa rondelle sur une partie fixe (le tout en rouge, exclu de l’analyse). Le tirant en gris au travers de la clame en jaune viens plaquer la chaise en rose sur une partie fixe en orange (indéformable, non recalculée).
Le matières sont du S355JR pour la chaise rose, du 42CrMo4 pour le tirant gris et la clame jaune.
Je suis soumis à 2 problèmes:
Le premier est que je n’arrive pas à déterminer de limite élastique à la matière elle même. Sur Total materia j’obtiens une fourchette de la RP0.2 de 390 à 650 MPa, alors que chez Aubert&Duval j’obtiens 1500 MPa en forgé…
que prendre comme référence?
La deuxième question que je me pose est que la contrainte max située au niveau de la clame est de 1064 MPa.
Plus j’affine le maillage, plus la valeur grimpe. Jusqu’où doit je l’affiner en ce cas?
Pour être plus complet, je reprend une NDC déjà faite où la personne qui l’a écrite disait que le tirant passait à 2046 MPa, sans préciser ou ni comment…
Si besoin de plus de précisions…
Je poste le modèle
Assemblage1.zip (46,8 Mo)
Merci
Bonjour @clement_merlin
Il vaudrait mieux que vous nous joignez l’ASM en joignant les résultats de l’analyse le tout par un pack and go zippé. En effet c’est seulement en regardant vos paramètres que l’on pourra vous donner un humble avis.
Cependant certains choses comme la légère déformation de la pièce rose alors que les équerres grises ne montrent pas de déformation attire mon attention
Confirmez moi que j’ai bien compris que ce qui vous intéresse c’est la pièce grise (la noire étant la tige du vérin ).
Pouvez-vous confirmer le nom des différentes pièces (par exemple CLAME ???)
Cordialement
1 « J'aime »
bonjour,
La noire et la grise sont une seule et meme pièce. La partie noire est juste une représentation de filetage.
Les 2 équerres qui ne se déforment pas sont mises « indéformables » dans le soft.
Le vocabulaire en lui même viens du client, je ne contredis pas ^^
Bonjour
J’ai un peu retarder ma réponse pour cause de plage à la mer.
Comme vous avez une version antérieure à la mienne je ne peux vous renvoyer le résultat de ma simulation.
C’est pourquoi je vous ai envoyer le rapport sous la forme PDF.
Mes commentaires !
1°) à partir du moment ou les équerres oranges sont réputées indéformable il n’aurait pas fallu les intégrer dans l’analyse. Vous noterez que dans l’analyse elles se déforment très légèrement sans que cela ait d’incidence sur le résultat.
2°) pour le solveur j’ai privilégié automatique plutôt qu’un solveur en particulier
3° ) pour les contacts j’ai utiliser solidaire
4°) compte tenu que les équerres sont réputées indéformables, elle auraient pu être exclu de l’analyse. Dans ce cas il suffisait de mettre déplacement fixes sur les surfaces d’appuis de la pièce orange sur la rose.
5°) dans les paramètre de maillage utiliser plutôt maillage basé sur la courbure (plutôt que maillage raccordé dans votre cas.
Pour le maillage pas nécessaire qu’il soit très fin puisque ce qui intéresse c’est le « tirant assemblage segment » !
6° vous n’avez pas défini de critère de ruine avant la sortie des résultats.
Dans vos résultats vous devriez rajouter le coeff de sécurité. Cela révèle que vous avez des zones à 2.18 , 2.42, et 2,87 sur le tirant ce qui me paraît un peu faible (mais je ne connais pas les conditions d’usages (chocs, vibration; etc…)
Egalement dans les résultats je vous suggère d’afficher la « dissection de conception » qui vous montrera pourquoi le résultats Von Mises à cette allure là.
De ce point de vue les fraisages des méplats qui servent pour le serrage à la clé ont des angles droits. Si vous prenez un fraise avec un rayon copieux cela va solidifier ces parties un peu faible.
Cordialement
Assemblage1-Statique 1-1.pdf (482,4 Ko)
1 « J'aime »
Bonjour,
Je me permet de retourner encore quelques questions suivants vos points:
- ok c’est logique j’aurais du y penser
- pourquoi en auto et pas présélectionner un solveur? (j’ai suivit le conseil du chef mais pas compris pourquoi…)
- ok
- ok
- pourquoi pas raccordé sur la courbure? J’avais compris que cela aidait quand on simulait un assemblage pour la continuité des maillages entre les pièces…
Je pensais également qu’un maillage plus fin aidait à localiser les concentrations de contraintes, notamment au niveau du tirant
- On part sur VonMises, mais je n’ai pas encore le retour du client pour la Re max du 42CrMo4 (le modèle est TQC evidemment).
Si vous parlez de ces angles droits des méplats
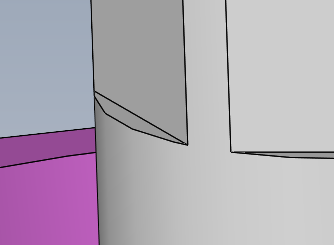
Mon chef m’a conseillé d’enlever les congés que j’avais mis pour la simulation justement, afin d’aviter des micro surfaces au maillage délicat.
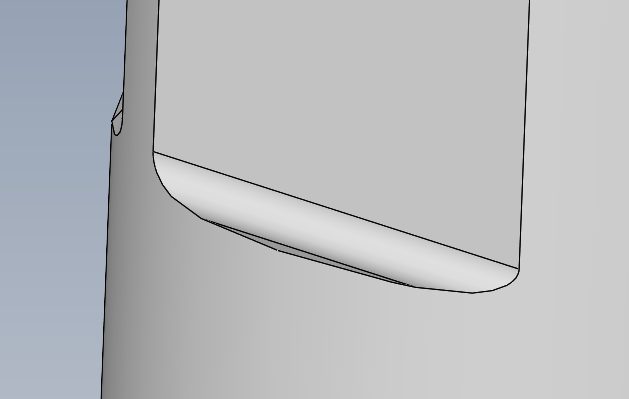
De plus dans votre NDC, je vois que les points de jacobien sont à 16pts, là où mon boss m’a conseillé de le mettre « aux noeuds ». Pourriez vous expliquer pourquoi avoir choisit cela?
Toujours dans votre NDC page 8 je vois un max à 981 MPa mais le graphe s’arrète au max à 337. Avez vous discriminé une partie du modèle? si oui comment et pourquoi? (en regardant le volume d’éléments géométrique cela représenterait moins de 0.01 % du modèle, ce qui si je me souviens bien de la formation peut être considéré comme étant « négligeable » ).
En refaisant le calcul de mon coté je me retrouve avec un volume de 23% au dessus de 337 MPa… je ne comprend pas d’où cela peut venir.
Assemblage1-Statique 1-3.pdf (634,3 Ko)
Petite aparté, lors de mes précédentes simulations, cette info de ratio "volume (élements/géométrique) = X% / X% n’était pas visible, y a t il une option que je n’aurait pas cochée?
J’essaye juste de comprendre ce qui est est le mieux , pas de descendre mon chef ou qui que ce soit on s’entend 
Merci à vous
Ne lui dites pas mais je ne suis pas d’accord avec votre chef 
Pourquoi ?
Tous les mécaniciens savent que les angles droits sont autant d’amorces de cassure ! d’où le rayonnage.
Dans la simulation de votre asm qui n’a rien de compliqué j’ai utiliser un maillage assez grossier sans que cela émotionne quiconque
Dans le cas de l’utilisation raisonnable de petits rayons il y a plusieurs façons de procéder
a) Mailler le modèle avec l’option « transition automatique ». Celle-ci applique automatiquement les contrôle de maillage aux petits détails, entités, trous et congés.
Ceci évidemment en fonction de la courbure de la géométrie. Le fait de raffiner le maillage permet d’obtenir des résultats de contraintes précis.
En deux mots :
Il convient de garder à l’esprit que toute résolution obtenue en utilisant une analyse PEF dépend de la manière dont le modèle a été maillé.
Également il convient de bien comprendre l’affinage (ce qui répond au passage à l’objection du chef sur les rayonnages des angles.
L’affinage permet de mieux maîtriser les contraintes singulières.
Je vous suggère de vous documenter sur les deux méthodes adaptatives « H » et « P » et de les comparer au type de résolution standard.
Dans votre rapport la dissection de conception n’est pas bonne il faut mettre le curseur plus loin pour vraiment voir les zones les plus sollicitées. Ce qui sera plus cohérents vis à vis du coeff de sécurité que je trouve un peu faible vu la traction exercée. (mais bon je ne suis pas the Chef 
Cordialement
PS : je ne sais pas ce que veux dire (le modèle est TQC evidemment). Mais si une tige aussi simple devient un confidentiel défense alors tout ce que je fait devient touchy 
Alors je dis que l’on défini pas une pièce pour faire plaisir à la simulation (suppression de rayons) mais en fonction de la plus grande solidité par rapport à l’usage qui sera fait de la pièce 
Supe rmerci,
J’avais justement trouvé ca qui parle des méthodes H et P
What is Convergence in Finite Element Analysis? SimScale
Je vais regarder tout ca de plus près.
Un grand merci en tout cas
TQC pour nous : Tel Que Construit = méthode de test traditionnelle visant à fabriquer et monter sur la machine AVANt de passer les pièces au calcul, et râler parce que ca casse 
Bonjour,
Quelques remarques:
- il semble que le design que vous calculez ne soit pas bon vu vos commentaires parlant de TQC et de casse. Ça serait bien de préciser où du coup
- il y a toujours des concentration s de contraintes dans les rayons, plus le rayon est petit (voire quasi nul) plus elle est élevée. Mailler avec une taille bien supérieure aux rayons réel minimise fortement les contraintes dans les résultats (on a vite un coeff de 2 à 5 entre un maillage ultra grossier et un maillage fin)
- supprimer les rayons là ou il n’y a pas de problème permet d’aller plus vite en maillage / calcul (mais de nos de jour ça sera de la femto seconde d’écart). Ca peut se comprendre surtout si la modif de maillage n’est pas sur la zone critique (je pense que c’est le cas et cela expliquerait pourquoi votre vieux chef vous a dit de virer les rayons (vieux car à l’époque les calcul EF prenaient des jours et simplifier le modèle faisait gagner des heures))
Si vous avez le soucis de casse au niveau du petit rayon ici
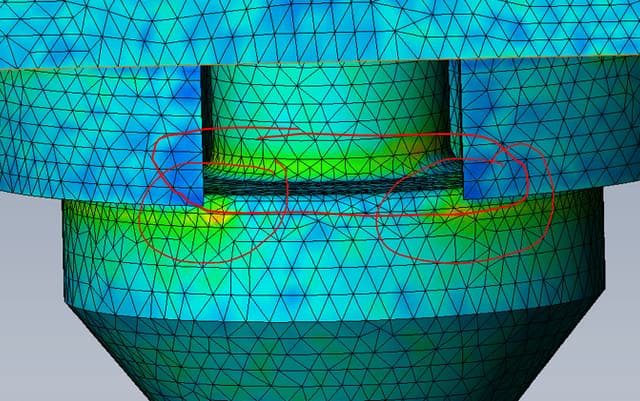
, vous avez effectivement intéret à avoir un minimum de 3 ou 4 éléments sur la longueur de votre rayon (taille de maille assez minusule du coup) si vous voulez avoir une idée de la vraie contrainte à cet endroit
A part sur le béton, on se fout généralement de la compression (vos deux cercles sur l’image du dessus), je doute que ce soit la zone du départ de rupture.
Le 42CrMo4 est un matériau devant subir un traitement thermique. suivant le procédé et la qualité du traitement, la taille de la pièce… le Rp0.2 et le Rm seront différent et seront aussi différent suivant si on est au cœur de la pièce ou en extérieur de celle ci.
Vous pouvez faire une dureté à coté de la zone cassée, il y a des équivalences dureté ↔ Rm
Les contraintes admissible par la pièce dépendent aussi de la gamme de fab : usinage puis traitements thermiques ou traitement thermique sur le brut puis usinage.
Si vous avez usiné un brut traité au préalable , il faut pas s’étonner que le matériau soit peu résistant au niveau du diamètre que j’ai entouré (c’est le cœur de la pièce donc un endroit moins traité thermiquement que l’extérieur de celle ci.
Autre question : est ce que la pièce travaille en fatigue ? Si oui quel type de fatigue ? suivant les matériaux, il faut vite diviser les contraintes admissible par 2 ou 3 si vous voulez atteindre des centaines de milliers de cycles.
L’analyse visuelle de la pièce cassée permet généralement de savoir si il y eu fatigue ou si il y a eu une casse nette sans fatigue préalable.
Vu le problème il faut faire l’analyse en gérant les contacts aux endroits critiques afin de permettre aux pièces de se décoller et de fléchir de façon réaliste. Avoir des contacts comme ceux ci :
ne vous permettra pas d’obtenir des résultats d’analyse corrects (toutes les pièces sont soudées entre elles → modèle beaucoup plus rigide qu’en réalité → contraintes beaucoup plus faible qu’en réalité)
PS : si le pb est dans la zone que j’ai entourée, augmenter le rayon au maximum (quitte à rajouter un rayon/chanfrein sur la pièce en C) est sûrement une bonne idée si vous voulez un design plus résistant (sans changer d’autres paramètres comme la gamme de fab ou les matériaux)
2 « J'aime »
Bonjour,
Pour les casses il s’agit d’une blague un peu ironique (mais globalement c’est dans l’esprit).
Je note pour les tailles de maillage des rayons, je vais jouer un peu avec voir les différents résultats que j’obtiens.
Ma cheffe n’est pas si vieille en plus XD mais je note la remarque.
Concernant la compression, on ne peut cependant pas dépasser la limite élastique pourtant? j’ai du mal à suivre sur cette partie…
Pour le traitement, j’ai un diamètre 150 sur le brut, et un diamètre usiné au plus fin de 66mm… En effet je me suis documenté sur le sujet je vais faire refaire les pièces en suivant un protocole de traitement plus carré.
La pièce n’est pas censée travailler en fatigue. je part déjà avec un coef 2
Pour les contacts je teste avec d’autres options.
Merci beaucoup