Hello
I've been looking for a function for some time that would allow me to create shape poses (3D printable) with a more or less complex volume size as a base data.
The Stamping or Impression functions allow you to create a " hollow " in a pose (see images), but the problem is that the base volume is trapped in the Pose volume. So we can imagine that it is impossible to place the piece on top in the installation.
Here as an example is a fitting of a tee which is a relatively simple shape, but my question is also valid for much more complex shapes.
The Material Removal by Volume Body Scan feature would have been optimal, but it does not support bodies with complex shapes...
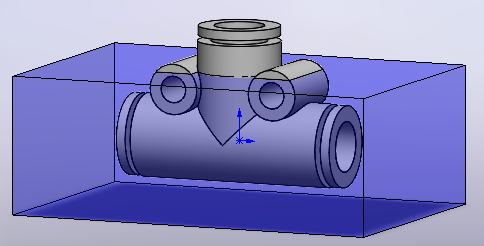
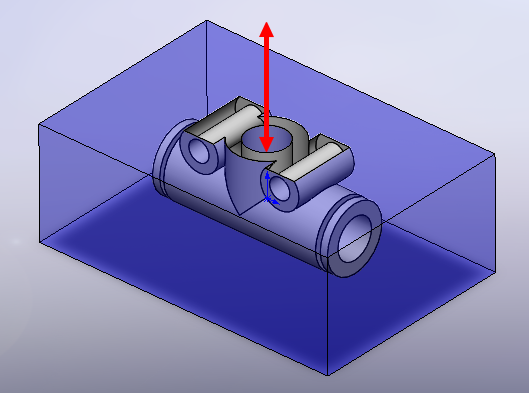
So I'm appealing to the community, do you know a solution?
If I have not been clear enough, please ask me for clarification.
Patrick
1 Like
Hello, are you trying to make a boolean? With the combine function it should do the job.
2 Likes
Hello
Faced with this problem, I found the solution with the feature function.
Even easier in 2024 because it is possible in this version to have the simplified version as a derived config.
→ the idea is to create a version of the connector without the openings (outer shape only) and use it with the combine/subtract or fingerprint function:
Alternatively, surface offset to 0, fill, and then use as a cutting tool with the surface removal function.
4 Likes
If I understand correctly, you're looking to have the silhouette of a body (a bit like its shadow).
Unfortunately, I don't have the solution, but I'll be happy if it exists.
1 Like
Yes, basically it's a bolean in subtraction of matter.
The " Material Removal-Scan with Material Body" function works, but only accepts single volume bodies for material removal tool. The example here is simple, but if I want to do a more complex body application, the " Material Removal-Volume Body Scanning" function does not work...
Image of the expected result (possible here because it is a simple body):
Now if I need to do a pose for a more complex room such as in the image below, it becomes much more complicated...
If you have a solution...
Thank you
2 Likes
Hello
You can already cut your piece in 2 and turn on top (it should help SW to do his calculations).
It doesn't work at all with your complex shapes?
If you don't need the detail of the propellers of the pinion, the easiest way is to add a revolution on your base part to remove the serrations and teeth).
This sprocket is just an example, I can't publish the 3D of my customers' products...
But thank you, it's a good idea to simplify the body as much as possible.
Nothing found to make your request.
Body scanning by material removal is effectively limited to bodies of revolution, so not possible for more complex parts.
Scanning a body is not allowed, otherwise it would be enough to do a sweep of this body (addition of matter) and then subtract it, by Boolean operation.
In my opinion, these are the only 2 reliable ways to get an exact result.
I tried subtracting a 1/2 piece but the result is not reliable because the part can be stuck in the block.
Basically not better.
2 Likes
SGDG: By using Motion, can we recover the envelope resulting from the movement of a part?
1 Like
As said: simplifying with Defeature, then it has the Silhouette Entity tool
( Silhouette Entities PropertyManager - 2022 - SOLIDWORKS Help) which can help to achieve the desired footprint, either through the imprint, material removal, or Boolean subtraction function.
3 Likes
This is a new feature for 2020.
Good to know that this function exists (finally)
2 Likes
Hello
I've already tried all this, without good results unfortunately.
With the removal of material with a silhouette, a flat bottom is obtained. You can't choose " up to the body, or to the surface ", it doesn't work if there are surfaces on " slopes "...
Not an easy exercise!
Hello
There are people whose job it is to make packaging and other principles of protection. Maybe there is a professional app that will solve your problem.
Otherwise, quickly on the net I found the AMCINDUSTRIE company which works in many industrial fields and makes all kinds of protections and probably also the study.
1 Like
Good evening
In the end, I don't think you can have anything automatic if the volume body scan doesn't work properly.
The easiest way is probably to put your base part in another part (via the Insert/Part menu), do an analysis of the draft on this part, add material wherever you have undercut, make your mark with this modified part.
2 Likes
This just means that you have to combine the 2 operations:
- silhouette for the " vertical " part
- Boolean subtraction operation between the part and the support for the rest.
1 Like
Are you talking about the recovery of the envelope resulting from the trip? Is that feasible?
Well, since we can get the sketch of the silhouette (see @Silver_Surfer's answer above), you can make an extrusion or a sweep of it.
You can then merge this volume with your piece to remove everything from your installation.
2 Likes
No, the result is a flat bottom, that's not the goal. It would need a base that follows the shape of the product, a bit like a mold.
Hello
Unless I'm mistaken, by using the molding tools and the surface we should be able to get out of it (there are functions that automatically " plug " holes in surfaces, to be checked on more complex shapes).
If there are people who do thermoforming on the forum, I think they will be able to answer the problem (I also came across a BTS CPI practical work that did this on SW2006-2007 but no details on how to make the impression). I have a vague memory of having done it during my studies but it goes back a bit a long time and a version of SW much further back (it must have been on 98 or 99, the functions were less evolved at the time).
3 Likes